Even minor malfunctions call for immediate stretch wrap machine repair to avoid bigger issues.
Even minor malfunctions call for immediate stretch wrap machine repair to avoid bigger issues.
Blog Article
Understanding the Importance of Timely Stretch Wrap Machine Repair Service Solutions
When it comes to extend cover equipments, timely fixings can make all the difference. What elements should you consider to ensure your makers remain in leading shape?
The Duty of Stretch Wrap Machines in Modern Production
Stretch wrap machines play an essential role in modern production by ensuring that products are safely packaged for transport and storage space. You rely upon these devices to offer stability and protection, preventing damage during transportation. When you make use of stretch wrap, you lessen the danger of products shifting or obtaining smashed, which can bring about pricey losses.
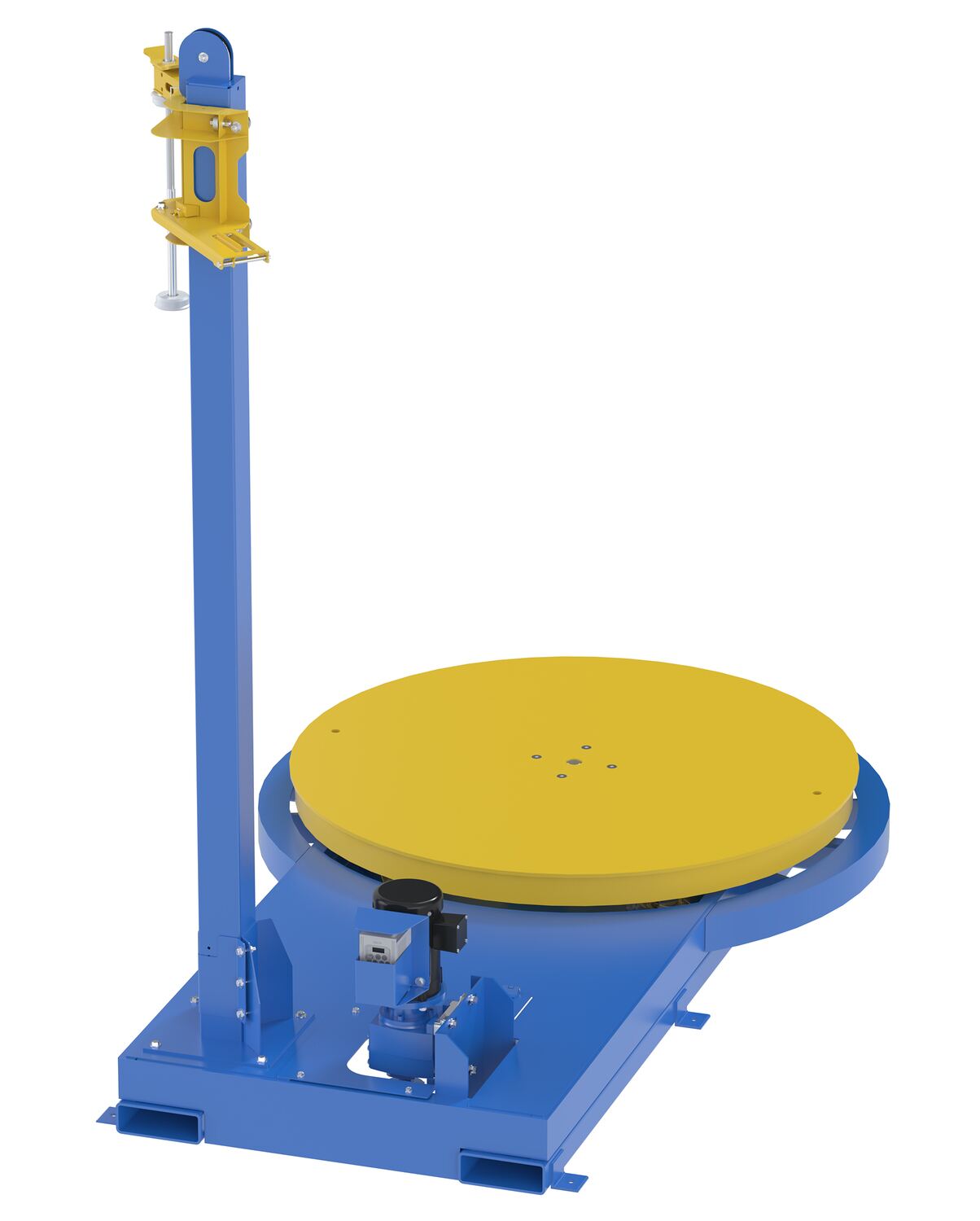
Moreover, utilizing stretch wrap makers can improve your overall supply chain performance. By improving the product packaging process, you decrease labor expenses and speed up shipment times, making certain that your consumers receive their items promptly. In today's hectic market, this advantage is essential.
Usual Concerns That Cause Device Downtime
When your stretch wrap equipment experiences downtime, it can typically be mapped back to mechanical failures or operator errors. Recognizing these common problems can assist you protect against costly interruptions. By resolving these points, you can keep your operations running efficiently.
Mechanical Failings and Breakdowns
When parts wear down or break, your stretch cover maker may halt suddenly, affecting performance. In addition, electrical failures can cause breakdowns in the device's control system, producing more delays. By prioritizing prompt repairs, you're not just minimizing downtime but also extending the life expectancy of your machine.
Driver Mistakes and Oversights
While operators play an essential function in the smooth performance of your stretch wrap maker, their mistakes and oversights can lead to considerable downtime. Common issues like improper loading, incorrect settings, and failure to keep track of cover tension can cause hold-ups and product damage. Ultimately, investing in operator training pays off by improving efficiency and prolonging your machine's lifespan.
The Financial Impact of Postponed Fixings
Postponing repair services on your stretch wrap maker can lead to substantial financial effects that ripple through your entire procedure. When your machine breaks down, performance plummets.
Furthermore, long term delays can escalate small issues right into major problems, needing more extensive fixings or perhaps complete substitute of the machine. This can stress your spending plan and interrupt capital. Hold-ups can additionally affect your delivery timetables, harming client fulfillment and potentially triggering you to lose organization to competitors. Eventually, prompt repair work are essential to preserving your profits and making sure smooth procedures. Don't ignore the economic effect of neglecting those repair service needs.
Advantages of Proactive Upkeep Programs
Prompt repair services can conserve you from costly downtime, however carrying out a positive upkeep program takes it a step further. This not just keeps your stretch cover maker running efficiently but additionally prolongs its lifespan.
Additionally, a proactive method improves productivity. With less interruptions, your workforce can focus on their jobs without the tension of abrupt maker failures. Plus, you'll likely save on repair prices, as minor concerns are normally much less expensive to deal with than significant repairs. Maintaining peak performance can enhance the top quality of your covered products, making sure consumer complete satisfaction. Over time, an aggressive upkeep program is an investment that settles via enhanced reliability and expense savings.
Recognizing Indicators That Your Machine Requirements Repair
As you run your stretch wrap device, it is important to remain alert for signs that indicate it may require repair work. If the film isn't stuck correctly or you notice irregular stress, your device could be malfunctioning.
Another indicator is a boost in downtime. If your device regularly stops or calls for modifications, it is time to examine. Maintain an eye on the device's rate; if it's slower than typical, something might be incorrect. Lastly, any noticeable damage like frayed wires or leakages should not be neglected. Promptly resolving these indications can protect against a lot more substantial issues down the line, guaranteeing your operations run efficiently.
Picking the Right Repair Solution for Your Demands
Exactly how do you choose the best fixing service for your stretch wrap maker? Consider their experience and know-how. Look for technicians that specialize in stretch wrap makers and have a tried and tested record. Inspect on-line reviews and reviews to determine client satisfaction.
Following, assess their feedback time. A trustworthy service must supply punctual assistance, as maker downtime can be costly. It's also necessary to understand if they supply emergency repair work.
Don't forget to inquire about warranties on repair services and parts. A respectable solution backs up their work, giving you satisfaction.
Lastly, contrast rates but avoid choosing solely based upon cost. Sometimes, the most inexpensive alternative might cause poor solution. By taking into consideration these variables, you'll discover a repair work service that meets your needs and maintains your stretch wrap maker running smoothly.
Strategies for Minimizing Stretch Cover Maker Downtime

Educating your drivers is one more vital method. Equip them with the understanding to recognize and address small glitches before they cause significant malfunctions. Motivate them to keep a log of any type of abnormalities, which aids in detecting issues quicker.
In addition, maintaining an inventory of crucial spare parts can substantially reduce downtime. When something breaks, having the best parts on hand suggests you won't have to wait on deliveries.
Last but not least, consider buying real-time tracking systems. These systems can signal you to performance modifications, enabling more info for instant treatment. By implementing these methods, you'll maintain your stretch cover maker running efficiently and successfully.
Regularly Asked Inquiries
Just How Usually Should Stretch Cover Machines Be Serviced?
You should service stretch wrap machines routinely, preferably every six months. If you observe any type of efficiency concerns or unusual noises, do not wait-- timetable maintenance immediately to avoid pricey malfunctions and ensure peak efficiency.
What Are the Regular Costs Connected With Stretch Wrap Equipment Repairs?
Normal costs for stretch cover machine repairs vary, but you may anticipate to spend in between $200 to $1,500 depending on the problem. Regular maintenance can assist reduce these prices and prolong your machine's life-span.
Can I Execute Standard Maintenance on My Stretch Cover Maker?
Yes, you can do fundamental upkeep on your stretch cover device. Routinely look for damage, clean the parts, and guarantee proper lubrication. Maintaining it in good form can extend its life expectancy and enhance efficiency.
Just how Do I Know if a Repair Work Solution Is Reputable?
To locate a reliable repair work solution, check on-line reviews, request for suggestions, and confirm certifications. A trustworthy solution will certainly offer clear price quotes, service warranty choices, and prompt interaction, guaranteeing you feel great in their know-how.
What Should I Do in Situation of an Emergency Maker Malfunction?
In instance of an emergency situation machine break down, you must promptly quit procedures, evaluate the issue, and call your fixing solution. Maintain critical get in touch with numbers convenient, and document the issue for efficient repairing when help arrives.
Conclusion
To sum up, recognizing the significance of timely stretch cover machine repairs can considerably improve your procedures. By resolving concerns without delay, you decrease downtime and prevent costly malfunctions. Accepting positive maintenance not just prolongs your devices's life-span but also enhances productivity and customer contentment. Bear in mind to stay attentive for signs of wear and choose a dependable repair solution to keep your devices running smoothly. Spending in these remedies repays in the future, ensuring your supply chain continues to be effective and effective.
Report this page